BOYUT TOLERANSLARI ve ALIŞTIRMALAR
1.TOLERANS NEDİR? Tolerans, günlük hayatta en basit ifadeyle “kabul edilebilir hata payı” demektir. Makinecilikte “makine parçası çalışırken görevini aksatmayacak şekilde ölçülerine verilen hata payı” na tolerans denir. Teknik Resme göre tolerans “en büyük ölçü ile en küçük ölçü arasındaki fark” a denir. Her mesleğin kendine göre toleransı vardır. Toleransın ne kadar olacağı mühendisler veya uzman kişiler tarafından belirlenir. En hassas makinelerde bile bir ölçünün tam olarak elde edilemediği görülmüştür. İş parçaları yapılırken kullanılan makinelerin yeni veya eski oluşu, ölçü aletlerinin hassaslığı, çalışılan ortamın ışık ve ısı durumu, işi yapan kişinin psikolojik durumuyla genel sağlık durumu ve göz sağlığı toleransı etkiler. Tüm bu etkenleri göz önüne alan uzmanlar tolerans sistemlerini geliştirmişlerdir. Parça üzerindeki ölçülerin kaba veya ince olmak üzere toleransları vardır. Kaba toleranslarda işçi fazla zaman ve emek harcamadan verilen ölçüyü elde eder. İnce toleranslarda ise işçi daha fazla zaman ve emek harcayarak verilen ölçüyü tolerans sınırları içinde elde eder. Genelde bir parçada ince tolerans az, kaba tolerans daha fazladır. Eğer tolerans verilmemiş olsaydı parçalar daha pahalıya imal edilirler, serbest piyasa şartlarında aynı işi yapan diğer firmalarla rekabet edemezlerdi. 2. BOYUT TOLERANS TERİMLERİ Boyut toleransının terimleri vardır bunlar çok iyi kavranmalıdır. Bu terimler TS EN ISO 286-1/2010 standardına göre aşağıya çıkarılmıştır. 1.Anma Ölçüsü (AÖ): Resim üzerine konulan ölçüye anma ölçüsü denir. Seçilen birim cinsinden sayısal değeri gösterir. Elde edilmesi istenilen en ideal ölçüdür. 2.Gerçek Ölçü (GÖ): Üretim sonunda elde edilen ölçüdür. Çeşitli ölçü aletleriyle ölçülerek bulunur. Üretim sonunda elde edilen ölçüyle kağıt üzerindeki ölçü farklı olabilir. 3. En Büyük Ölçü (EBÖ):Bir parçanın yapılabileceği en büyük ölçüdür. 4. En Küçük Ölçü (EKÖ):Bir parçanın yapılabileceği en küçük ölçüdür. En büyük ve en küçük ölçüler uzmanlar tarafından tespit edilir. İş, bu iki ölçü arasında yapılırsa iş doğru yapılmış demektir. 5.Tolerans (T): Bir parçanın yapımında izin verilen ve parçanın çalışmasına engel olamayan hata payıdır. Daha açık ifadeyle en büyük ölçüyle en küçük ölçü arasındaki farktır. Şekil 1’ de boyutların en büyük ve en küçük ölçüleri verilmiştir. Ø90 ölçüsüne göre toleransı bulmak için T=90.1-89.9=0.2 çıkarma işlemi yapılır. Burada tolerans T=0.2’ dir. Ø60 ölçüsüne göre toleransı bulmak için T=60.2-59.8=0.4 işlemi yapılır ve tolerans T=0.4’ dir. Şekil 2’ de delik ölçüleri görülmektedir.
Şekil 1:En büyük ve en küçük ölçüler Şekil 2:Delik ölçüleri 6. Sapma: Anma ölçüsüyle, en büyük veya en küçük ölçü arasındaki farka denir. 7.Üst sapma, anma ölçüsüyle en büyük ölçü arasındaki farka denir ve ES harfleriyle gösterilir. Hesaplamayı Ø90 ölçüsüne göre yapalım:
ES=EBÖ-AÖ=90.1-90=0.1 işlemiyle hesaplanır. Burada üst sapma ES=0.1’ dir. 8.Alt Sapma: Anma ölçüsüyle en küçük ölçü arasındaki cebirsel farka denir ve EI harfleriyle gösterilir. Hesaplamayı Ø90 ölçüsüne göre yapalım: EI=EKÖ-AÖ=89.9-90=-0.1 işlemiyle hesaplanır. Burada alt sapma EI=-0.1’ dir. Şekil 3’ de Ø60 ölçüsüne göre sapma değerleriyle diğer ölçüler gösterilmektedir. Burada 0 çizgisi anma boyutundan geçen çizgidir. 9.Gerçek Sapma: Üretim sonucunda elde edilen ölçüyle anma ölçüsü arasındaki farka denir.
Şekil 3:Ø60 için sapmalar ve ölçüler 3.ALIŞTIRMALAR 1. Mil: Silindirik bir parçanın dış kısmıyla silindirik olmayan bir parçanın paralel dış yüzeylerine mil denir. Şekil 4-a’ da bir silindirik parçanın Ø60 ve Ø90 ölçüleriyle Şekil 4-b’ deki tüm ölçüler mil sınıfına girmektedir.
Şekil 4:”Mil” örnekleri 2.Delik: Silindirik bir parçanın iç kısmıyla silindirik olmayan bir parçanın paralel iç yüzeylerine delik denir. Şekil 5-a’ da parçanın silindirik iç kısmındaki Ø60 ve Ø90 ölçüleriyle Şekil 5-b’ deki tüm iç ölçüler delik sınıfına girmektedir.
Şekil 5:”Delik” örnekleri 3.Alıştırma :Birbirine takılması gereken mil ile delik arasındaki ölçü farklılığına alıştırma denir. Boşluklu, sıkı ve belirsiz alıştırmalar vardır. 4.Boşluk (B): Bir montajda mil çapı delik çapından küçükse aradaki pozitif (+) farka boşluk denir (Şekil 6). 5.En Büyük Boşluk (EBB):En büyük delik ölçüsü ile en küçük mil ölçüsü arasındaki pozitif (+) farktır. 6.En Küçük Boşluk (EKB):En küçük delik ölçüsü ile en büyük mil ölçüsü arasındaki pozitif (+) farktır. Şekil 7’ de EBB ve EKB ölçülerinin meydana gelmesi görülmektedir.
Şekil 6:Boşluk (B) Şekil 7:Boşlukların meydan gelmesi 7.Sıkılık (S): Bir montajda mil çapı delik çapından büyükse aradaki negatif (-) farka sıkılık denir (Şekil 8). Burada delik ölçüsünden mil ölçüsü çıkarılmaktadır. 8.En Büyük Sıkılık (EBS):En küçük delik ölçüsü ile en büyük mil ölçüsü arasındaki negatif (-) farktır. 9.En Küçük Sıkılık (EKS):En büyük delik ölçüsü ile en küçük mil ölçüsü arasındaki negatif (-) farktır. Şekil 9’ da EBS ve EKS ölçülerinin meydana gelmesi görülmektedir. 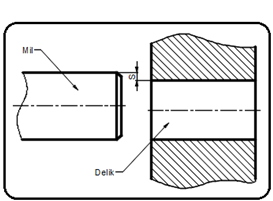
Şekil 8:Sıkılık (S) Şekil 9:Sıkılıkların meydana gelmesi 4. ALIŞTIRMA ÇEŞİTLERİ 1.Boşluklu alıştırmalar: Daima boşluk sağlayan bir alıştırmadır. Mil ölçüsü delik ölçüsünden küçüktür. Düşük devirde dönen kaymalı yataklarda, perçinleme işlemlerinde, merkezleme amacı gütmeyen pimli birleştirmeler örnek olarak verilebilir. 2.Sıkı alıştırmalar: Daima sıkılık sağlayan bir alıştırmadır. Mil ölçüsü delik ölçüsünden büyüktür. Parçalar yerlerine kuvvet uygulanarak takılırlar. Dişli çarklar, yatak burçları, silindirik pimler sıkı alıştırmayla yerlerine takılırlar. 3.Belirsiz alıştırmalar: Delik ve milin ölçüsü birbirine çok yakın olduğunda meydana gelen alıştırmadır. İnsan kuvvetiyle itildiğinde kayabilen ve takılabilen parçalar için kullanır. Delme yüksükleri, değiştirilebilen dişli çarklar, merkezleme pimleri, merkezleme flanşları örnek olarak verilebilir.